SCHWAN'S
Get to know our growing global brands
- Big Daddy's
- Edwards
- Mrs. Smith's
- MINH
- Red Baron
- Freschetta
- Pagoda
- Tony's
Featured Careers
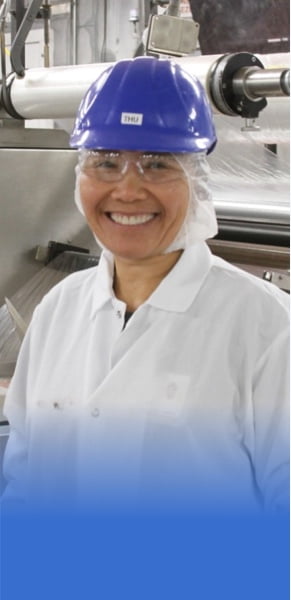
MANUFACTURING
MANUFACTURING & LOGISTICS
Employees work in a fast-paced environment that puts the safety of employees and customers above everything else.
Team members can grow in their positions, learn new skills, and advance their careers. We offer opportunities in manufacturing and logistics at over a dozen facilities across the United States.
Learn More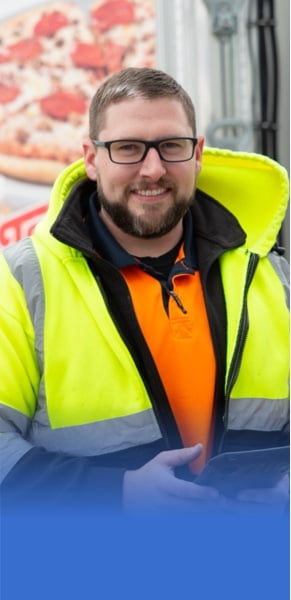
RETAIL SALES
RETAIL SALES
Our retail team members are passionate about making a difference in the lives of our customers. As a member of our team, you'll have the opportunity to work with our innovative products while also being recognized for the hard work and value you'll bring on a regular basis.
Learn More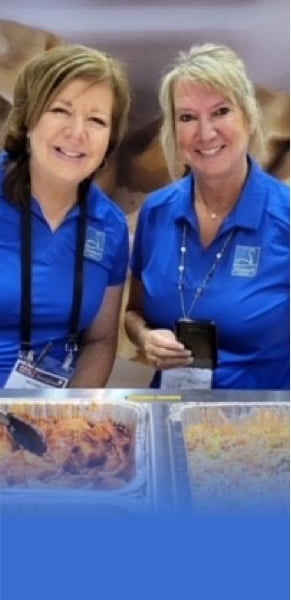
FOOD SERVICE SALES
FOOD SERVICE SALES
Our sales professionals work in a fast-paced team environment. We proudly seek exceptional candidates for field leadership, route sales, and delivery positions across the United States.
Learn More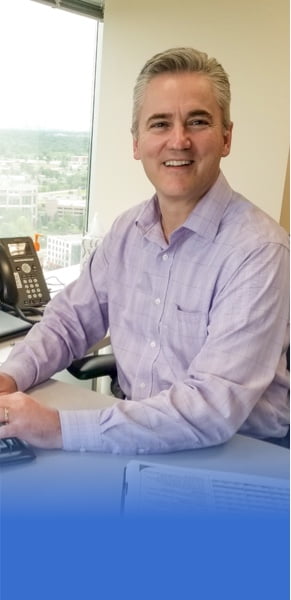
CORPORATE
CORPORATE
Our corporate teams use a diverse set of specialized skills to support the teams that make, sell, market and deliver our foods. Corporate functions include areas like general management and leadership, marketing, product innovation and development, operations, finance, information technology, human resources, legal, communications and much more.
Learn MoreEarly Careers
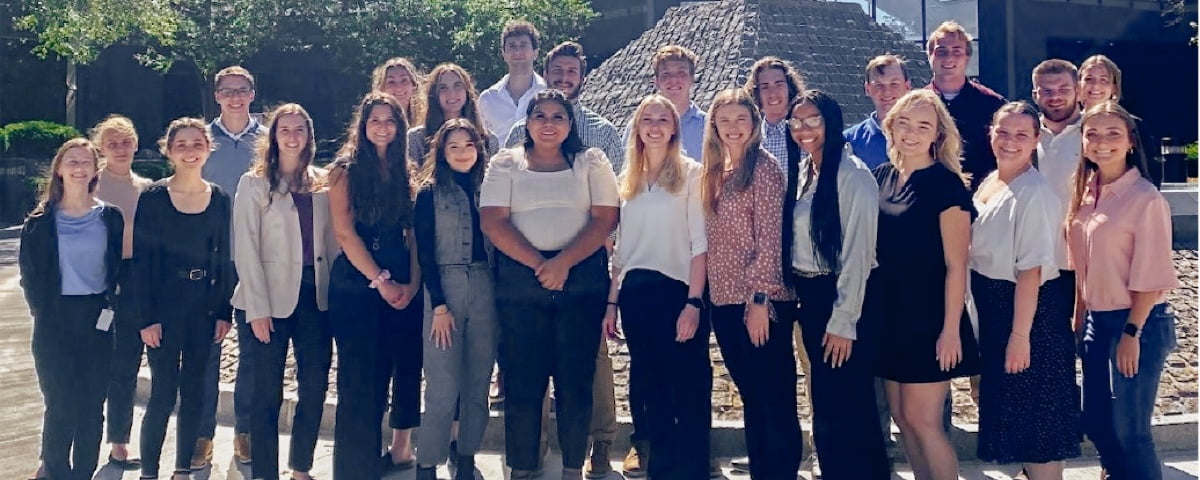
From Accounting to Sales and Marketing to Food Science, we offer a broad range of internships and entry-level positions in a learning environment that’s energetic and supportive. Join us and take on real-world challenges, projects and assignments that impact our business and jumpstart your career.
Learn MoreSee what’s happening @ our table
SIGN UP FOR JOB ALERTS
Join our Talent Network and get Schwan's news and job alerts delivered to your inbox.